When following a required workflow in a software application, few things are more frustrating to the user than attempting to convert a file and having the operation blocked due to incompatibility. The user will need to repeat their work to output in a different file format or may even need to utilize a third-party tool for conversion. This loss of functionality is not only aggravating but will require more time and effort to get to the desired result.
A more common example is one that most everyone has come across at some point: the incompatibility across PCs and Macs. Most everyone who uses a PC also uses Microsoft Office for applications such as Microsoft Word. If you’re sharing your Word document with someone who uses a Mac and doesn’t have Microsoft Office for Mac installed, it creates frustration, delays, and the potential for errors. Unfortunately, while a converter is available, it does not produce the best quality.
Uniformity within software applications significantly impacts the process, outcome, and time spent in development. The key to achieving uniformity with files and documents within a software application is interoperability.
What is Interoperability?
Interoperability is a characteristic of a product or system in which the product or system works with other products or systems without any restrictions.
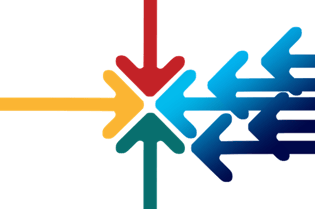
Oracle further defines interoperability as:
Interoperability reduces or eliminates the problems of islands of automation. It enables business processes to flow from one application to another. Interoperability enables one system to work with another, in near real-time fashion, to share critical business information. Interoperability options become the glue between systems and applications.
Interoperability comes in many forms. One form, in particular, is CAD data translation software. This type of software enables end-users to work with imported 3D data as easily as if it were created natively in the application and export the 3D data for downstream engineering applications.
The Need for Interoperability Within Software
To truly understand the need for interoperability within software, we’ll discuss examples that demonstrate the roadblocks that appear when there is a lack of uniformity present.
Let’s say an end-user is utilizing a 3D software application to design an aircraft. This is a complicated design because it includes the structure, engines, avionics, control systems, interior/cabin arrangements, and various other sub-systems. Each of these sub-systems are composed of parts, and the assemblies of these parts are provided by a myriad of vendors, all using a wide range of CAD and other digital information systems. In the absence of file interoperability, Original Equipment Manufacturers (OEMs) and multi-level tiered suppliers cannot communicate with one another intelligibly.
Additionally, when it comes time to output a file, the user may have to find and implement several different third-party tools for conversion. This may be costly and difficult to manage for internal departments and procurement departments. Even if third-party tools are found that do the job, high-quality conversions are not guaranteed across many different tools.
With today’s extended global supply chains, all of which depend on CAD data, it’s important that there’s an easy way for the files within 3D CAD software applications to communicate with each other.
![]() |
3D InterOp offers other attributes of data. For example, visibility and layer information from the source CAD system are available such that the data can be presented in the same form as it was being used in the original system. |
3D File Formats Across Different Industries
A 3D file format is used for storing information about 3D models as plain text or binary data. More specifically, a 3D file format encodes the 3D model’s geometry, appearance, scene, and animations.
Any industry whose applications require digital engineering (CAD) data needs the ability to convert files or read/write. As you can imagine, each industry has its own popular 3D file formats. These industry-specific formats came from either the inception of the software or were adapted over the years for practical reasons.
With so many software companies, the advancement of technology, and ever-changing demands between industries, many different 3D file formats are being used today. Because of this extreme variety across industries such as CAD, CAM, CAE, and BIM, it’s not hard to see how interoperability is hindered.
On the subject of 3D data translation, Wikipedia states:
The CAD systems currently available in the market differ not only in their application aims, user interfaces, and performance levels, but also in data structures and data formats. Therefore, accuracy in the data exchange process is of paramount importance, and robust exchange mechanisms are needed.
We’ll briefly go into different file formats for three industries: CAD, CAE, and BIM.
CAD File Types:
The Computer-Aided Design (CAD) industry includes the following native file formats:
- DWG: Native file format for Autodesk’s AutoCAD program and most popular 3D CAD file format
- BLEND: A scene description format from the 3D modeling and animation software, Blender
- X_T: Parasolid file format. File extension contains 3D CAD file information like geometry, topology, and color from a drawing
- SLDPRT and SLDASM: SolidWorks file extensions, short for “SolidWorks Part” and “SolidWorks Assembly”
- IPT and IAM: Autodesk Inventor formats for parts and assemblies
- SKP: SketchUp’s beginner-friendly way to create and share CAD files
- Model: 3D modeling format used by CATIA; used for building molds, dies, composites, and other types of models.
- IGS: An IGS file is a graphics file saved in a 2D/3D vector format based on the Initial Graphics Exchange Specification (IGES). It can store wireframe models, surface or solid object representations, circuit diagrams, and other objects.
- & Many More!
CAE File Types
The Computer-Aided Engineering (CAE) industry includes the following file formats:
- INP: Edit and run by the command line
- DAT: The text output file that will contain results
- ODB: The binary output file that will be read during post-processing to view graphical results
- LOG: Keeps a text record of all processes
- MSG: Lists the progress of the analysis and provides some messages about why an analysis might have crashed
- STA: A summary of the information contained in the .msg file; this is useful for monitoring the status of long-running jobs during their computation
- CATPart: Contents of the file include 3D geometry, dimensions, and metadata
BIM File Types:
The Building Information Management (BIM) industry includes the following file formats:
- DWG: This format is almost universally accepted by most model viewing/authoring programs.
- DXF: Similar to the DWG, DXFs can be larger in file size but are also layer-based and a very commonly accepted format on most platforms
- IFC: Industry Foundation Classes. Information-rich BIM files that can be opened by programs including Autodesk Revit and Navisworks
- RVT: Autodesk’s proprietary format for Revit files; can only be opened in Revit
- NWD: Autodesk’s proprietary format for Navisworks files
![]() |
Example of Building Information Modeling (BIM) software application |
How Robust Interoperability Improves Software Workflows
Having robust interoperability support in software removes tedious translation steps that bog down workflows. When a part is imported into an application, the process should be a quick one-step with high-quality results and no loss of data. Although the norm decades ago, step-by-step translations are very time-consuming and come with the potential for loss of data.
![]() |
Example of part in 3D InterOp |
Today, the efficient, high-quality 3D data translators inside 3D InterOp provide quick translations without data loss. There’s no need to incur the extra costs and aggravation of the past approach.
With so many highly-engineered systems in today’s CAD world for industries, such as aerospace, automotive, industrial, agriculture, buildings, infrastructure, simulations, virtual reality, the potential to reach a point where few of the software applications talk to each other is a real challenge. Without a solution, developers are forced to purchase licenses for many different kinds of CAD software, which is prohibitively expensive and unrealistic. 3D InterOp is the solution that keeps the conversation going by translating the communication efficiently and effectively.
Case Studies: 3D InterOp Supporting Extensive Breadth of 3D CAD Formats
![]() |
Ultimaker software for 3D printing. Image courtesy of Ultmaker.com |
Ultimaker’s software, CURA, produces solid body meshes used for 3D printing. Ultimaker integrated 3D InterOp into CURA specifically to support an extensive breadth of 3D CAD formats. Ultimaker customers can now directly import 3D Designs into CURA and are relieved of tedious translation steps to convert from the myriad of 3D CAD formats to formats for 3D printing. As a result, users can quickly upload a wide range of 3D CAD design files of the most recent CAD versions directly in their native form and convert them all without the need for any additional CAD application.
In another example, when new sub-systems (e.g., software-controlled electric steering systems) for the automotive industry are developed, OEMs like BMW or Toyota often use CATIA. But not all of the myriad of global suppliers can afford a CATIA installation and might use SolidWorks instead. As a result, automotive supply chains worldwide rely on 3D InterOp to exchange and process 3D engineering data during development.
High-Quality Data Translation with 3D InterOp Ensures Software Workflows Never Stalls
When your 3D application has a high-quality data translation component built into it, the benefits include high-quality file-to-file translation, speed, reliability, and adaptability. Quite simply, with a solution like 3D InterOp, your company realizes less cost, less hassle, and increased efficiency. Universal format support through data translation keeps each of the systems talking and moving forward through the process towards success.
Are you looking to expand or revamp your interoperability capabilities? Learn more about 3D InterOp and reach out to our team to start your journey!