Release 2021 1.0 Enables Automatic Measurement Planning, Process Automation, and Expands Support for Mesh-Based Data
Release Highlights:
- Enable Automatic Measurement Planning with 3D InterOp's CAD PMI Import
- Enhance MBD Review with 3D InterOp's STEP AP 242 Graphical PMI Export
- Further Enable Faster Review of Large Models
- Build Process Automation with CGM's Feature Recognition
- Build Powerful CAD Simplification Workflows with CGM's Automatic and Interactive Tools
- Expand Your Support of Mesh-Based Data Regardless of Quality with CGM Polyhedra
- 3D ACIS Modeler: Serving the World's Leaders in 3D Modeling with Solutions to Industrial Challenges
- Other Highlights in 2021 1.0
Enable Automatic Measurement Planning with 3D InterOp’s CAD PMI Import
Easy-to-Use, market-leading metrology software enables measurement planning rather than cumbersome and archaic measurement programming. Using Spatial’s 3D InterOp, build metrology software that automatically generates measurement plans and preserves design intent by importing PMI (Product Manufacturing Information) from 3D CAD models into your software.
3D InterOp can import both semantic PMI (machine-readable) and graphical PMI (human-readable), along with Views, Captures, and links to 3D geometry.
Leveraging 3D InterOp, your CMM/Metrology application users can:
- Review PMI and associated geometry objects in 3D with cross-highlighting (graphical PMI). Reduce clutter on the screen by activating the CAD file’s Views and Captures.
- Query the values and tolerances of these PMI in the application itself, to build further automation (semantic PMI).
- Automatically generate measurement plans for a sub-set or all of the imported PMI objects.
- Avoid human errors associated with re-entering PMI values.
- Automatically update measurement plans when a CAD model is updated upstream, leveraging 3D InterOp’s CAD Associativity.
Additionally, developers of such CMM/Metrology applications are freed from the burden of supporting regular CAD version updates when they use 3D InterOp v/s building their own CAD import solutions.
In Release 2021 1.0, 3D InterOp supports such PMI functionality for STEP AP 242 and JT. This is in addition to existing support for PMI in CATIA, NX, Creo and SOLIDWORKS CAD formats.
NIST STEP AP 242 model imported using 3D InterOp
Enhance MBD Review with 3D InterOp’s STEP AP242 Graphical PMI Export
Enable your customers to achieve MBE Maturity Index Level 4 by allowing them to export STEP AP242 models annotated with lightweight, viewable PMI.
Using 3D InterOp, your engineering application can export graphical PMI linked to 3D geometry with pre-defined views to STEP AP 242 files. This allows collaboration between designers and manufacturing engineers or suppliers. They can simultaneously develop the product’s design as well as manufacturing methods.
A designer using your application can export a CAD model with PMI to STEP AP 242, delivering explicit dimensions, tolerances, and manufacturing annotations to peers while protecting their IP. This STEP model can then be used in a following design-for-manufacturing review with members of teams such as process engineering, quality control or fabrication, to provide early feedback on production concerns or anticipate production requirements about the designed part.
STEP AP 242 model with PMI, written/exported using 3D InterOp
Further Enable Fast Review of Large Models
Selective Import for Optimal Performance
3D InterOp’s selective import ability lets you optimize your data preparation application for handling large CAD models.
Last release, we made considerable improvements to CATIA and SOLIDWORKS import.
This release we have improved JT visualization import performance by as much as 2x, for large models.
Your application can start by just importing the data required for visualization of the large CAD model, which with latest improvements is typically in the order of seconds or a few minutes (see below for more details) versus much longer for a full B-rep import. This means that your users can start reviewing large models soon after uploading them in your application.
While your users review the model, your application can start loading exact B-rep data in the background. It can also allow your users to isolate and selectively import exact B-rep for just a few parts in the large assembly, and continue the workflow without having to re-start the process.
Build Process Automation with CGM’s Feature Recognition
New Feature Types for Manufacturing
CGM Modeler’s native feature recognition adds new support for chamfer recognition in addition to robustness improvements for filleted pads, pockets and slots. Most 3D CAD models designed for machining have chamfers and fillets, with Release 2021 1.0 you can use identified features to:
- Analyze models for manufacturing time and cost.
- Simplify parts by removing chamfers or fillets when they are not necessary for part function.
- Fix manufacturability concerns without access to the feature tree; for example: removing and reapplying chamfers to meet standard CAM tool sizes on native (CATIA, SOLIDWORKS etc.) CAD as well as standard CAD (IGES, STEP) models. Imported data in native CAD is also supported for such recognition and defeaturing.
This release also supports sheet metal cut-out recognition.
![]() |
![]() |
Chains of Chamfers (left); Sheet Metal Cut-Outs (right); Models Courtesy of SOLIDWORKS. |
Build Powerful CAD Simplification Workflows with CGM’s Automatic and Interactive Tools
Feature Recognition & Defeaturing Robustness Improvements
Most feature recognition in CAD and CAM applications fail when features such as holes are more complex than standard configurations such as Bore Holes, Counter Bore Holes and Counter Sunk Holes. With Release 2021 1.0, CGM Modeler’s native feature recognition can identify and remove complex, interacting, or otherwise non-standard holes using geometric properties. Additionally, CGM Modeler’s defeaturing can handle interactive workflows to remove combined features.
This part when meshed for simulation with its complex holes has over 187,758 triangles. With the holes removed for a bulk analysis, it has only 38,570 triangles.
Expand Your Support of Mesh- Based Data Regardless of Quality with CGM Polyhedra
Identify and Fill Complex Holes
Mesh-based data often comes with quality issues, precluding further analysis or manufacturability. Complex 3D surfaces with a lot of local variation, makes smoothly filling gaps difficult. Release 2021 1.0 release provides a robust and advanced algorithm to fill non-planar holes leveraging local topology. CGM Polyhedra offers not just flat patching of holes, but also refinement and smoothing to produce high quality results that conform to local curvature.
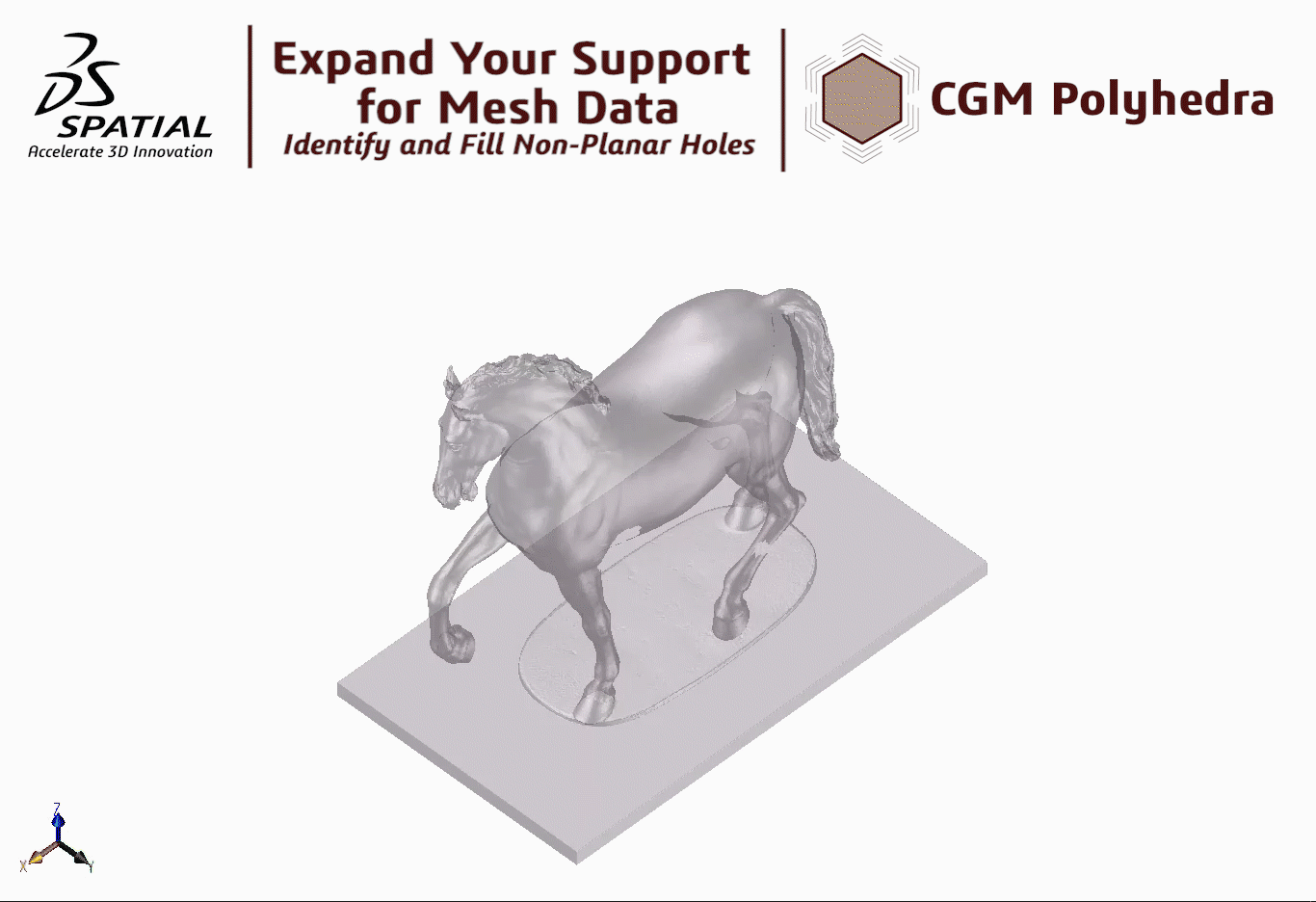
At each release the ACIS team improves upon its quality as a proven modeler and acts as a solution advisor to leaders in the CAD/CAM/CAE industry while expanding support for ACIS customers to benefit from Spatial’s ecosystem of technology.
In Release 2020 1.0, the ACIS team improved performance of workflows requiring precision; such as workflows providing data preparation for manufacturing of imported data. Read below for information on improvements to healing, exact bounding box calculations and slicing.
Leveraging an eco-system of technology: improve support for imported data into ACIS
Significant performance improvements in the ACIS Checker, and healing of gaps at tight tolerances, leads to faster import of CAD models into ACIS. Performance was improved at multiple check levels: duplicate vertices check (performed at level 10+) is now up to 38x faster, and improper face intersections check (performed at level 70) is now up to 2x faster. Healing gaps of 10-6 values is now up to 1.3x faster.
ACIS as a proven modeler: faster computations with every release
The bounding box computation with exact mode is now faster by caching and eliminating unnecessary calculations through recognition of faces and edges that contribute to the exact box. This improves performance for all workflows relying on the most precise bounding boxes. Improvements are most significant on very large models with non-analytic geometry, as shown below, at up to 21x.
Your solution advisor: new ACIS functionality that the CAD/CAM/CAE communities need
With Release 2021 1.0, Spatial has added new support to slice exact B-rep models at multiple locations using a single ACIS call. Slicing is also now multi-threaded, leading to a cumulative speed of up to 2x. This enables the use for more precise exact models in manufacturing workflows.
More details can be found in the ACIS release notes.
Other Highlights in 2021 1.0
3D InterOp:
- SOLIDWORKS Threads and Holes Import
- Extract Mesh information as Visualization Data from DXF/DWG files in 3D InterOp CGM*
- Progress Notifications for Assembly Product Structure and Part Visualization Imports
- IFC Structural Elements GUIDs Import
- Updates to documentation to expand the coverage of the new UConnect interface
- 3 new C# samples in the package that guide you through import-export, manufacturing import and visualization import workflows
- Updated CAD Version Support:
- Creo 7
- Solid Edge 2020, up to MP10
- Support of AutoCAD 2021
- Support of Inventor 2021
- Support of SOLIDWORKS 2021
- Support of CATIA V5 R2021
- Support of NX1926 series up to NX1938 (*2020 1.0.1 HF in October, 2020)
Refer to the 3D InterOp Release Notes for a complete list of updates
CGM:
- New operator to flatten open sheet bodies as well as transfer wires either way between the folded and unfolded/flattened version of sheet bodies. This can be useful for design applications modeling soft materials.
- 3D Precise Mesh works with any MeshGems version 2.4 to 2.11.
- 3D Precise Mesh for CGM has new methods to provide increased customization of the surface mesh.
Refer to the CGM release notes for a complete list of updates
ACIS:
- ACIS modeler now supports chamfer network chain detection as well as removal. Adding chamfer detection has enhanced the robustness and performance of chamfer removal.
- ACIS-HOOPS bridge has been upgraded to support HOOPS 3DF 25.00.
- 3D Precise Mesh works with any MeshGems version 2.4 to 2.11.
Refer to the ACIS release notes for a complete list of updates