3D Modeling
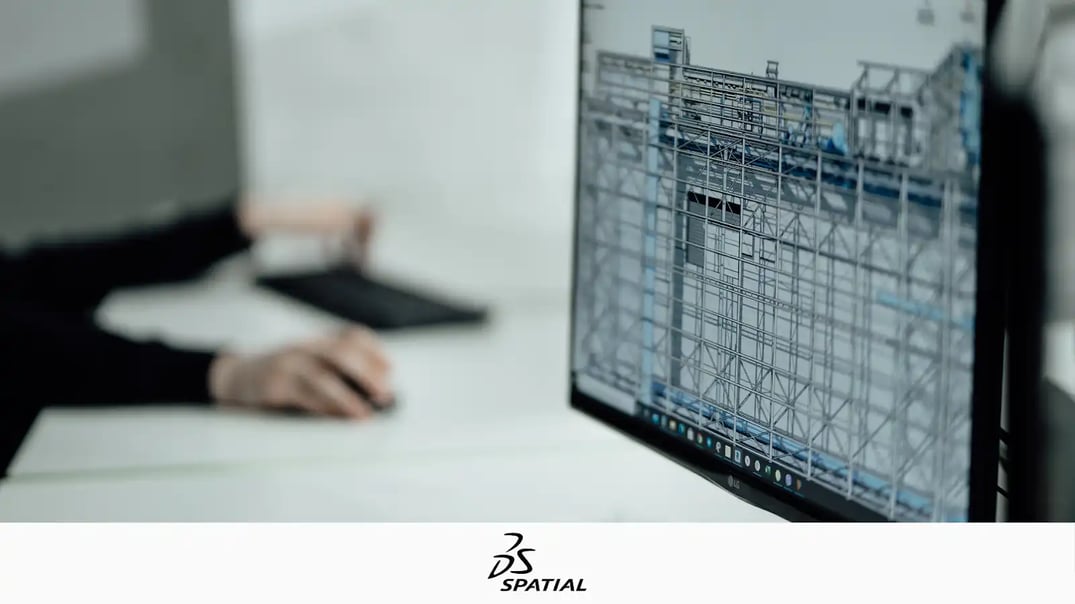
What Is Digital Manufacturing and 3 Benefits You Need to Know About
Spatial Team | 15-07-2022
What is digital manufacturing? Here’s a simple digital manufacturing definition: the process of using computer systems to support and improve manufacturing operations.
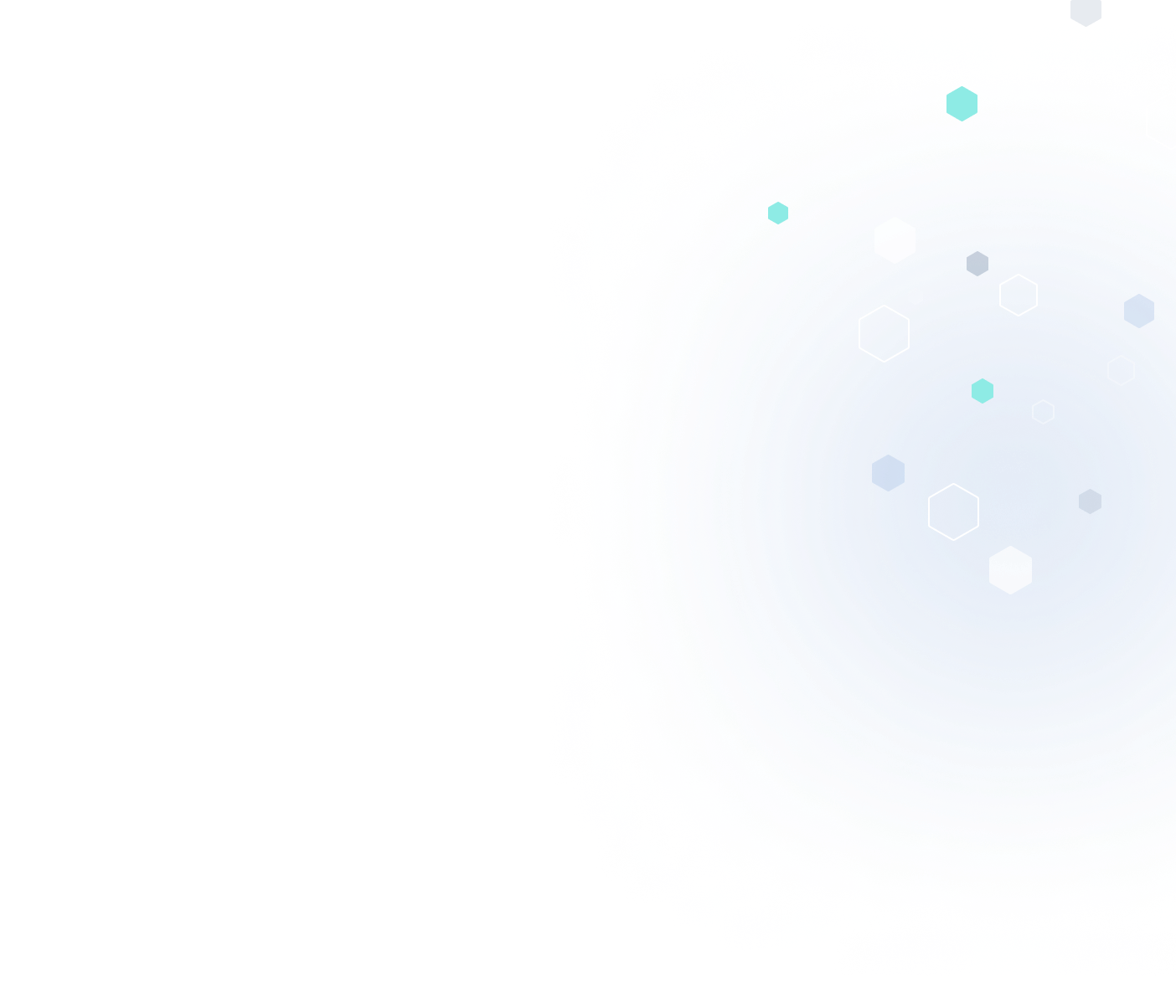
Categories
All Posts 3D Modeling 3D Software Development Kits Additive Manufacturing 3D InterOp 3D Interoperability CGM Modeler 3D ACIS Manufacturing & Fabrication 3D Data 3D Visualization Building Information Modeling (BIM) 3D Precise Mesh Hybrid Modeling 3D Printing CGM Polyhedra Cloud & Mobile HOOPS Visualize HiddenBodyRemoval Meshing insider spatial
5 min read
What Is Digital Manufacturing (and its Benefits)
Author:
Spatial Team
What is digital manufacturing? Here’s a simple digital manufacturing definition: the process of using computer systems ...

5 min read
How 3D Components Impact Software UX
Author:
Spatial Team
Software components are like the stage crew at a big concert performance: the audience doesn’t see them, but their ...
.jpg?width=386&height=386&name=Application%20Lifecycle%20Management%20(1).jpg)
4 min read
How to Reduce Development Time and Maximize Revenue During Application Lifecycle Management
Author:
Spatial Team
When you hear the term, Application Lifecycle Management (ALM), you likely think about the process that a software ...

9 min read
The Process of SLS in Additive Manufacturing
Author:
Spatial Team
SLS in Additive Manufacturing is used to convert 3D CAD designs into physical parts, in a matter of hours.

8 min read
3D Printing for Additive Manufacturing - What You Need to Know
Author:
Spatial Team
There’s a lot of confusion around what the terms additive manufacturing and 3D printing mean.
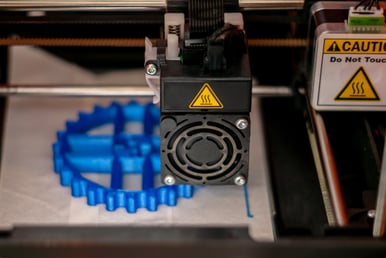
4 min read
The Additive Manufacturing Process
Author:
Spatial Team
Additive manufacturing, often referred to as 3D printing, is a computer-controlled process for creating 3D objects.

5 min read
3 Core Components of CFD Analysis
Author:
Spatial Team
Computational Fluid Dynamics (CFD) is a type of analysis that provides insight into solving complex problems, and ...

2 min read
What is a WRL File?
Author:
Spatial Team
WRL files are an extension of the Virtual Reality Modeling Language (VRML) format . VRML file types enable browser ...

3 min read
The Main Benefits and Disadvantages of Voxel Modeling
Author:
Spatial Team
Voxels are to 3D what pixels are to 2D. Firstly -- let’s examine what pixels actually are. Everything you see on your ...
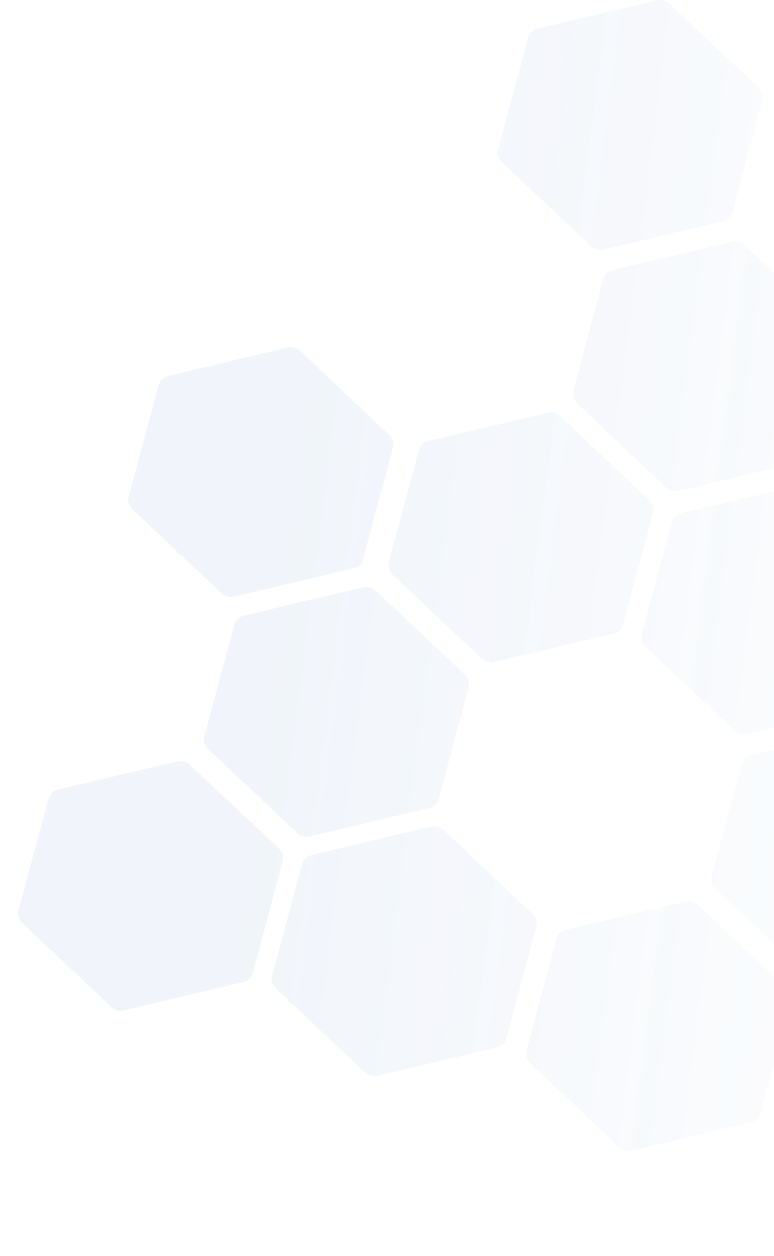