When coming from a standard format, very often that data has to be repaired or improved, and Spatial does that as part of our interop product.
Now that we are dealing with tessellating data as STL, we are going to walk through common pathologies and errors that we find in these files.
Understanding the Effects of STL File Problems
STL Data with Missing Triangles
The first is missing data, missing triangles.
If you are missing triangles then you don't have a watertight solid volume. Being a watertight solid volume is really the first requirement of all slicing algorithms, be it from Spatial or some other company.
So, you have to fill in these holes where triangles are missing, small holes like the one below are pretty simple to fill, but we see a lot of data with holes that have complete surfaces missing from a part of this questionable STL data that is out in the wild.
Avoiding STL Data Errors Such as Flipped Triangles
The next common error we call Flipped Triangles.
Triangles all have to be oriented the same way with the right-hand rule, in order to determine that you have you a closed volume. Often, we see files that do not comply with that.
So you need algorithms that understand the geometry to identify and correct this to get all the triangle pointing outwards to create this watertight volume.
Understanding Intersecting Triangles in STL Data
Very often the basis for the STL file that gets generated out of the computer-aided design (CAD) system is the triangulation that was created for visualizing it.
To put a 3D model on the screen you have to tessellate it into triangles, i.e. the language that the graphic card speaks. Every CAD system has the ability for that, so you can create triangles that look pretty good on the screen but it has flaws the user cannot see.
This is OK for 3D visualization. But, when we need to actually slice that for 3D print preparation, such errors will disrupt the slicing and make it unreliable.
So in this case you have bad cognitivity from the triangles or small triangle that is flipped over.
It may not be noticeable when you are just visualizing the part, but it will cause problems when you try to manufacture from that data. This is another problem we must repair in the STL before moving towards manufacturing.
Intersecting or Mating Surfaces
Another common thing that we see are parts that look good at first, e.g. the model below of a spark plug.
When look at the mesh and tessellation, this looks pretty healthy. It doesn't have the problem of missing data or badly intersecting triangles.
However, when we look further it was actually modelled as an assemble. There are 3 or 4 parts that overlap. If you slice this directly to print it, you are going to have problems.
This is because at the boundary where the multiple parts intersect, you are going to have redundant laser paths or redundant machine paths.
Now if it SLM or SLS then the laser will go over the part too many times and it will change the the behaviour of the materials. If it is a FDM type of process that you are going to try and print the same beads of material in the same place, it will probably just cause a mess of the printer or a mess of your part.
So, this is another way where someone requested that this model be printed, but it is not ready to be printed yet. You need 3D modeling capability to resolve this assembly into a single part volume that is ready to be printed.
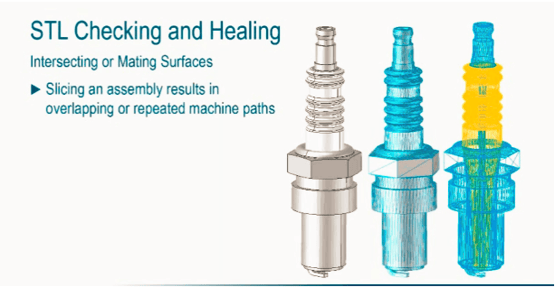